IN-SITU RECOVERY TECHNOLOGY
In-situ recovery (ISR) technology is a proven method of extracting uranium from deposits in sandstone rock that cannot be extracted by traditional methods - open pit or underground mines.
Currently, ISR is the most commonly used method of uranium production. It is also used to extract other metals, such as copper.
The way the ISR method works is that a leaching solution is injected into the deposits through wells and circulated to dissolve the uranium. The uranium-containing solution is then pumped out of the deposits and sent to a processing plant where it is mixed with resin. Next, the uranium particles are separated from the resin, purified, concentrated and packaged as the final product in drums for transportation. The leaching solution, stripped of uranium, is reinjected into the deposits, making ISR a closed-circuit cycle.
This approach causes minimum surface disruption and generates no tailings or waste rock. Capital costs are low (compared to traditional mining methods), and ISR is often the most efficient method of mining low-grade uranium deposits.
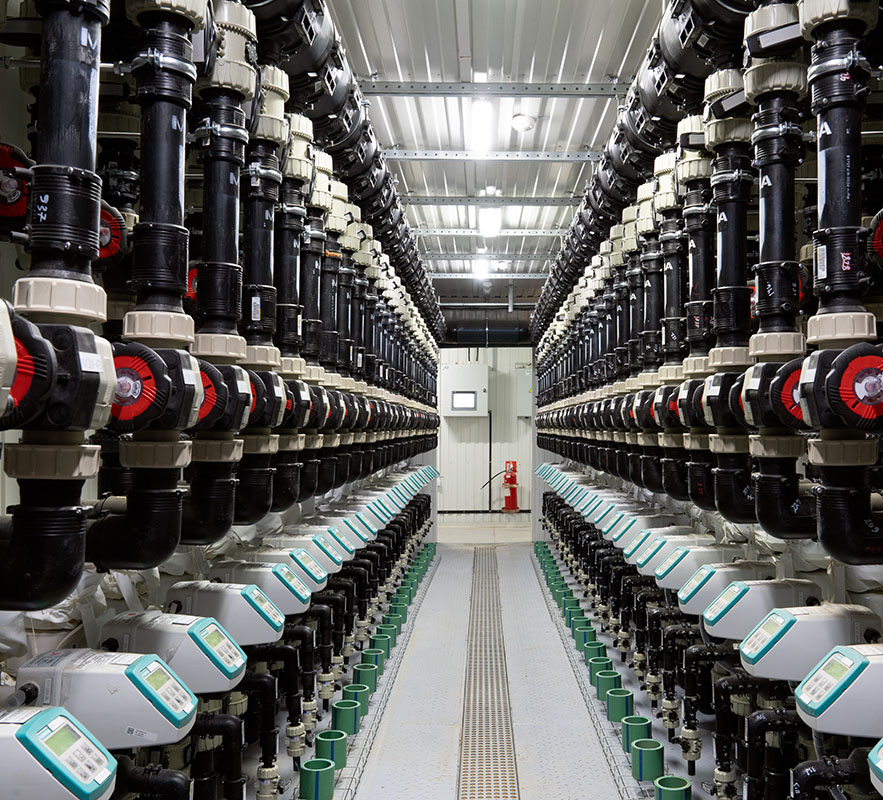
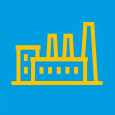
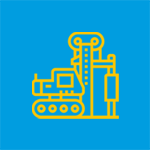
ADVANTAGES OF ISR
- ISR is a popular method because it has a number of economic, technical and environmental advantages over traditional mining methods:
- Reduced capital costs (no mining fleet, no ore crushing, simplified processing plant)
- Reduced operating costs (no blasting or excavation)
- Greater flexibility of production capacity
- No tailings and ore
- No pits, waste dumps or tailings dams
- Minimum visual disturbance to the environment
- Minimum noise, dust and diesel emissions (minimal use of heavy machinery, no haul roads)
- Reduced carbon dioxide emissions
We welcome the fact that Kazakhstan has signed the Paris Agreement on climate change. The use of ISR technology reduces carbon emissions compared to oil and gas companies and mine operations, which use more carbon-intensive methods.
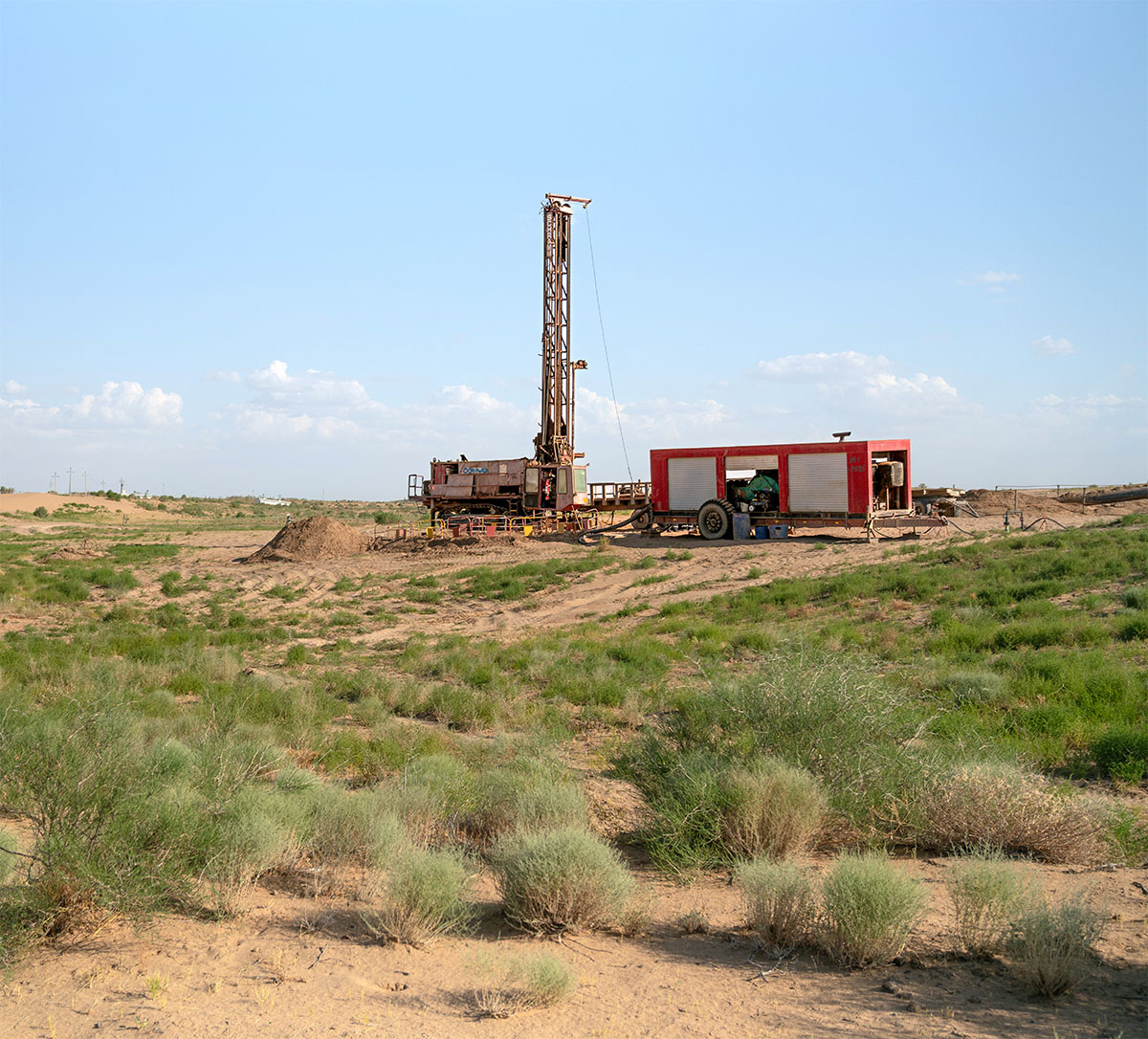
KATCO INNOVATIONS ON ISR
Many innovations have been introduced in the company to develop the ISR technology.
These include the OSIDEM tool for real-time production monitoring and the HYTEC tool for modelling the ISR process not only for operations but also for environmental protection.
ISR REMEDIATION
Environmental monitoring and remediation are important at all stages of ISR project.
KATCO invests in best practices and innovations, in the process of continuous improvement of the environmental protection measures.
It has become clear while working in Kazakhstan that the impact of acidification on aquifers due to leaching solution naturally wanes over time.
The process whereby a mineralized aquifer returns to its original state is called natural attenuation.
KATCO, with the support of Orano Environmental Research and Development department, is conducting a research to improve the characteristics of this natural attenuation.
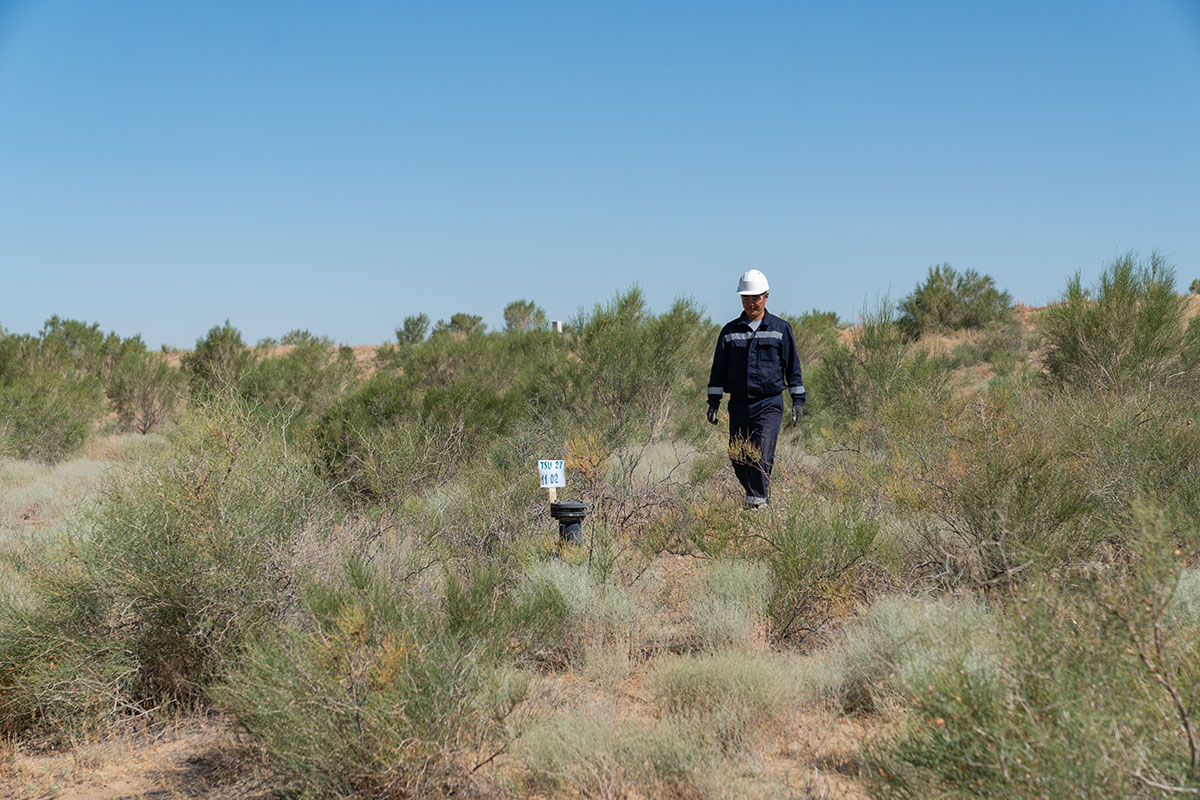